Lupine limon in časopisi za kreme in plastično embalažo
Vesna Žepič Bogataj, Tecos: »Ne razvijamo bazičnega znanja, temveč znanje, ki je takoj uporabno in prenosljivo na industrijsko raven.«

Odpri galerijo
Trije Tecosovi EU projekti Life in prototipi novih izdelkov iz recikliranih materialov. Foto Brane Piano
V Razvojnem centru orodjarstva Slovenije Tecos z evropskim projektom Life Ceplafib od julija snujejo predelavo odpadne plastične embalaže in časopisnega papirja v materiale za izdelke v embalažni in avtomobilski industriji ter v gradbeništvu. Tecos kot vodilni partner projekta sodeluje s finsko družbo Ecopulp, poljskim inštitutom ITB in španskim Aitiip ter s slovenskima podjetjema Adria Mobil in Omaplast.
Že pred tem je Tecos sodeloval pri dveh projektih Life – Citrus in Baqua. S koordinatorico projekta Ceplafib in vodjo laboratorija za aplikativne materiale v Tecosu, dr. Vesno Žepič Bogataj, smo se pogovarjali, katere tehnološke rešitve in znanje uporabljajo pri projektih, kako so si zamislili ponovno uporabo tako različnih odpadkov, kot so olupki in surovine pulpa citrusov, ostanki rastlin bananovcev ter odpadne plastične embalaže in časopisnega papirja za nove materiale v visokotehnoloških proizvodnjah. Pa tudi, da znotraj EU ni omejitev – tako bo pri Ceplafibu proizvodna linija za predelavo novih materialov iz recikliranih surovin v Španiji, prototipni izdelki za notranjo opremo avtodomov bodo izdelani v Sloveniji, demonstracijski izdelki za gradbeni sektor na Poljskem, industrijska embalaža iz recikliranih surovin pa na Finskem. Ceplifab je tipičen model krožnega gospodarstva. Ob zmanjšanju stroškov za izdelke iz novih materialov sta cilja tudi povečanje količin predelanih odpadkov na 40 odstotkov ločeno zbranih odpadkov ter zmanjšanje emisij toplogrednih plinov za proizvodnjo sedanjih izdelkov za prav toliko.
Žepič Bogatajeva je v celjskem razvojnem centru orodjarstva od leta 2011; najprej je delala kot mlada raziskovalka, od leta 2015, ko je obranila doktorat, se ukvarja z evropskimi projekti. Doktorirala je iz bioznanosti s področja lesa in biokompozitov na Biotehniški fakulteti Univerze v Ljubljani.
To me je zanimalo. Po osnovni izobrazbi sem inženirka gozdarstva, v Tecosu je največ strojnikov in prišla sem s čisto drugačnim ozadjem – znanjem o lesu, upravljanju gozdnih ekosistemov in zaščiti naravnih virov. Razvoj lesno-polimernih kompozitnih materialov sem usvojila z doktoratom, kar je bila specializacija na nanokompozitnih materialih, kjer smo ojačali biopolimerno matrico z nanocelulozno materijo. Ceplafib smo privedli do stopnje, da je tudi industrijsko zanimiv.
Pred leti smo izpeljali mednarodni projekt E! 2819 Factory Ecoplast, ki je dobil nagrado za najboljšo Eurekino zgodbo. Na trg smo vpeljali nov material, lesno-polimerni kompozit na osnovi poliolefinske matrice, pravzaprav polipropilena, ki je najbolj razširjen tehnični polimer v industriji plastike. Ojačali smo ga s celuloznimi vlakni, a ni še šlo za reciklirane materiale kakor zdaj pri Ceplafibu, temveč za primarne surovine. Material smo uporabili v aplikativni demonstraciji izdelave zvočnih sistemov z zelo dobrimi akustičnimi lastnostmi. Znanje o spajanju lesa in plastike ter izhodnih lastnosti smo že imeli, saj je tudi sedanji direktor Aleš Hančič svojo doktorsko dizertacijo obranil prav s področja določitve in optimizacije mehanskih lastnosti biopolimernih kompozitnih materialov s pomočjo mikromehanskih metod. Vemo, kako se material obnaša, kakšne mehanske lastnosti lahko pričakujemo, kam jih lahko umestimo v industrijskem sektorju oziroma katerim gospodarskim panogam bi takšen material bil zanimiv.
Potem smo se povezali še z reciklatorji oziroma predelovalci določenih odpadnih materialov. Ta ideja se nam je zdela dobra za izvedbo mednarodnega projekta sploh zdaj, ko smo v obdobju tranzicije krožnega gospodarstva.
Seveda. Spraviti v en kompozit les in plastiko je težko, ker komponenti nista kompatibilni – les je hidrofilen, plastika je hidrofobna. Na lesnih komponentah morajo biti narejene nekatere modifikacije, bodisi kemijske na površini celuloznih vlaken bodisi mehanske z dodatki kompatibilizatorjev v obliki granulata, da dobimo ustrezno spojnost komponent in homogeno obliko izhodnega kompozita. Kemični modifikaciji prve ali druge materialne komponente se v tem projektu načeloma izogibamo, ker racionalno ni prenosljiva v nobeno industrijo …
Sodelujejo torej kemiki, procesna industrija za ekstruzijsko pripravo kompozitnega granulata, potem potrebujemo orodjarje, da izdelajo ustrezna orodja, sledijo še tehnične odobritve materialov po določenih standardih in certifikatih. Potrebujemo torej obsežno interdisciplinarno znanje.
Vsi okoljsko naravnani projekti Life, ki smo jih v Tecosu prijavljali, so naravnani tako, da so na koncu čim bliže trgu. Ne razvijamo bazičnega znanja, temveč je to po koncu projektov takoj uporabno in prenosljivo na industrijsko raven. Ceplafib smo predstavili našim podjetjem in iskali nekoga, ki bo znal reciklirati odpadno plastiko, nekoga, ki lahko pripravi surovine za ojačitve, regenerirana celulozna vlakna iz odpadnega papirja ali iz naravnih ligno-celuloznih virov poljedelskih odpadnih produktov … Našli smo ga na Finskem, kjer se veliko podjetij ukvarja s predelavo lesnih surovin.
To sta bila prva partnerja. Nato smo iskali tehnološke centre, da pomagajo pri procesnih tehnologijah in nazadnje še, koga bi takšni izdelki zanimali. Vzpostavili smo stik z Adrio Mobil, ki v avtodome in prikolice vgrajuje okoli 35 odstotkov komponent iz plastike. Zanimalo jih je. Njihove glavne zahteve so bile povezane z mehansko in strukturno trdnostjo materiala, kar jim narekujejo standardi o varnosti voznikov in potnikov. Za končne izdelke smo predvideli pokrivne panele za skrite inštalacijske sisteme, notranji dekor, ker jim je bila všeč vidna struktura lesnih vlaken v plastiki. Druga aplikacija uporabe novega kompozita bo izdelava distančnih profilov za dvojni pod v avtodomih. Zdaj so iz lesa. Serijska proizvodnja brizganih distančnikov iz lesno-plastičnih kompozitov bo okoljsko boljša.
V Omaplastu pravijo, da je reciklirani polipropilen cenejši. Novi kompozitni materiali bodo cenejši, ker bomo uporabili cenejše reciklirane surovine. Če za polnilo uporabimo vlakna iz časopisnega papirja, dobimo tudi lažji material in porabimo 30 do 40 odstotkov manj plastike.
Da. Naš glavni cilj je obvarovati primarne vire, saj je plastika v osnovi narejena iz naftnih derivatov. Z vnosom reciklatov v končni kompozitni material zmanjšamo ogljični odtis. Izdelali pa bomo tudi študijo ustvarjenega odtisa od surovine do končnega izdelka.
Gre za notranje akustične panele, odrske panele, ki bi zamenjali USB-plošče. V gradbeništvu je uporaba lesno-plastičnih kompozitnih materialov že znana. Izdelujejo na primer fasadne plošče, terasne pode, obrobe bazenskih kompleksov … Novost tega projekta je uporaba lesno-plastičnih kompozitov, ki so v celoti izdelani iz recikliranih surovin.
Ne gre za primerljivo embalažo. Podjetje Ecopulp iz Finske zdaj obvladuje izdelavo celuloznih embalažnih izdelkov z vročim stiskanjem, ker pa v svojih produktnih linijah potrebuje tudi trša embalažna ogrodja, se mu je skozi projekt Ceplafib ponudila priložnost za uvedbo trših, vendar kljub vsemu v celoti reciklabilnih materialov.
Od 2015 do lani nam je v treh zaporednih letih uspelo pridobiti evropska sredstva za zagon treh do okolja prijaznih Life projektov in ugotavljamo, da se je tudi slovenska industrija zbudila in sledi krožnim zgodbam. V prvih projektih iz let 2015 in 2016 je Tecos sodeloval kot partner, pri sedanjem pa je koordinator. Prvi projekt, Life Baqua, ki ga koordinira španska univerza s Kanarskih otokov, temelji na uvajanju krožnih rešitev za izrabo bananinih odpadkov za razvoj produktov v ribogojskem in plastičarskem sektorju. Na Kanarskih otokih imajo ogromne plantaže bananovcev, oleseneli stebelni ovoji palm pa se v velikih količinah leta dolgo kopičijo na tleh. Ideja projekta Baqua je predelava olesenelih ostankov bananovcev v vlakna za ojačitev strukturno polimernih izdelkov v avtomobilski industriji ali industriji bele tehnike. Odpadni produkti bananovcev bodo obenem predelani v granulirano hrano za ribe na bližnjih morskih gojiščih.
Novomeško podjetje Ambi-Metalplast, ki izdeluje brizgane plastične dele za avtomobilsko industrijo, je partner tega projekta in želi v svoj nabor vključiti tudi izdelke iz takšnih sonaravnih materialov.
Drugi projekt, Life Citruspack, se je začel leta 2016. Pobudnik je špansko podjetje AMC, ki izdeluje sokove iz agrumov in ima ogromno odpadnih surovin. Vodilni partner projekta je raziskovalni center AITIIP iz Zaragoze, sodelujejo pa še raziskovalni in industrijski partnerji iz Španije, Belgije, Slovenije in Francije. S pomočjo kemične ekstrakcije bodo iz odpadnih ostankov citrusov, olupkov in pulpe, pridobljene netopne antioksidantske spojine, ki bodo uporabljene kot dodatek kozmetičnim produktom za efekt pilinga ter surovinska baza za izdelavo naravnih ojačitev v biorazgradljivih polimernih osnovah za izdelavo biokompozitne embalaže za plastenke za sokove in lončke za kreme.
Da, bo pa ločeno zbran spet uporaben za recikliranje. Evropa zahteva, da morajo biti do leta 2030 vsi izdelki iz plastike reciklabilni. Naš material bo reciklabilen vsaj kot polnilo.
Ni tako slabo, kakor včasih mislimo. Slovenija je pri reciklaži vseh vrst odpadkov tretja v Evropi po deležu zbranega stekla, plastike, papirja … Pri reciklaži plastike prednjačita Nemčija in Češka, reciklirajo je več kot 45 odstotkov. Slovenija je že med 40 in 45 odstotki. Novomeški Omaplast, ki je reciklator plastike, dobiva odpadno embalažo večinoma iz tujine, v Sloveniji le desetino. Potrebuje čiste materiale, in ne mešanih vrst plastik, te pa je najlaže dobiti iz industrije.
Kitajska je januarja letos uvedla zeleno zaveso in prepovedala uvoz 24 vrst odpadkov. Včasih je bila zlata jama za izvoz odpadkov, od tam pa smo dobivali poceni komponente. Zdaj ni več tako. Odpadne plastike iz tujine sploh nočejo reciklirati, niti odpadnega kartona. To je lahko težava, lahko pa tudi nova priložnost za evropsko območje. Lahko se bo pojavilo več podjetij, ki se bodo začela ukvarjati z reciklati. Tudi Omaplast v tem vidi priložnost.
Slovenija nima veliko proizvajalcev granulatov iz odpadne plastike. Eden izmed ciljev našega projekta je, da Omaplastu odpremo poti do kupcev v Evropi tudi tja, kjer še niso prisotni, in tudi do boljšega sodelovanja s slovenskimi proizvodnimi podjetji. Zato smo k Ceplafibu povabili še druga podjetja in doslej se jih je pridružilo dvanajst. Med njimi je osem slovenskih, ki jih novi material zanima – ali kompozit iz reciklirane plastike in časopisnih vlaken, morda samo reciklirani plastični granulat … Med njimi so Gorenje, Bokri, Isokon, Koplast, Plastoform, Skaza, Snaga, Vivapen … Povabilo je odprto, zmogljivosti imamo dovolj, da lahko novega materiala izdelamo več. Ne torej samo za potrebe našega projekta, temveč za vse, ki bi želeli preizkusiti nov kompozit v svojih utečenih produktnih linijah.
Znanje se je razvijalo in nalagalo že prej, je pa tri leta za nov material z vso akreditacijo na trg in uporabo na procesnih strojih res kratko. Mi smo po tem, ko smo vedeli, da so vsi potrebni materiali na voljo, nov kompozit razvili v letu dni, še dve leti pa sta potrebni za validacijo.
Že pred tem je Tecos sodeloval pri dveh projektih Life – Citrus in Baqua. S koordinatorico projekta Ceplafib in vodjo laboratorija za aplikativne materiale v Tecosu, dr. Vesno Žepič Bogataj, smo se pogovarjali, katere tehnološke rešitve in znanje uporabljajo pri projektih, kako so si zamislili ponovno uporabo tako različnih odpadkov, kot so olupki in surovine pulpa citrusov, ostanki rastlin bananovcev ter odpadne plastične embalaže in časopisnega papirja za nove materiale v visokotehnoloških proizvodnjah. Pa tudi, da znotraj EU ni omejitev – tako bo pri Ceplafibu proizvodna linija za predelavo novih materialov iz recikliranih surovin v Španiji, prototipni izdelki za notranjo opremo avtodomov bodo izdelani v Sloveniji, demonstracijski izdelki za gradbeni sektor na Poljskem, industrijska embalaža iz recikliranih surovin pa na Finskem. Ceplifab je tipičen model krožnega gospodarstva. Ob zmanjšanju stroškov za izdelke iz novih materialov sta cilja tudi povečanje količin predelanih odpadkov na 40 odstotkov ločeno zbranih odpadkov ter zmanjšanje emisij toplogrednih plinov za proizvodnjo sedanjih izdelkov za prav toliko.
Kitajska je januarja uvedla zeleno zaveso in prepovedala uvoz 24 vrst odpadkov. /…/ To je lahko težava, lahko pa tudi nova priložnost za evropsko območje.
Žepič Bogatajeva je v celjskem razvojnem centru orodjarstva od leta 2011; najprej je delala kot mlada raziskovalka, od leta 2015, ko je obranila doktorat, se ukvarja z evropskimi projekti. Doktorirala je iz bioznanosti s področja lesa in biokompozitov na Biotehniški fakulteti Univerze v Ljubljani.
Kako ste se kot gozdarka znašli v Tecosu?
To me je zanimalo. Po osnovni izobrazbi sem inženirka gozdarstva, v Tecosu je največ strojnikov in prišla sem s čisto drugačnim ozadjem – znanjem o lesu, upravljanju gozdnih ekosistemov in zaščiti naravnih virov. Razvoj lesno-polimernih kompozitnih materialov sem usvojila z doktoratom, kar je bila specializacija na nanokompozitnih materialih, kjer smo ojačali biopolimerno matrico z nanocelulozno materijo. Ceplafib smo privedli do stopnje, da je tudi industrijsko zanimiv.
To ni prvi tovrstni Tecosov projekt.
Pred leti smo izpeljali mednarodni projekt E! 2819 Factory Ecoplast, ki je dobil nagrado za najboljšo Eurekino zgodbo. Na trg smo vpeljali nov material, lesno-polimerni kompozit na osnovi poliolefinske matrice, pravzaprav polipropilena, ki je najbolj razširjen tehnični polimer v industriji plastike. Ojačali smo ga s celuloznimi vlakni, a ni še šlo za reciklirane materiale kakor zdaj pri Ceplafibu, temveč za primarne surovine. Material smo uporabili v aplikativni demonstraciji izdelave zvočnih sistemov z zelo dobrimi akustičnimi lastnostmi. Znanje o spajanju lesa in plastike ter izhodnih lastnosti smo že imeli, saj je tudi sedanji direktor Aleš Hančič svojo doktorsko dizertacijo obranil prav s področja določitve in optimizacije mehanskih lastnosti biopolimernih kompozitnih materialov s pomočjo mikromehanskih metod. Vemo, kako se material obnaša, kakšne mehanske lastnosti lahko pričakujemo, kam jih lahko umestimo v industrijskem sektorju oziroma katerim gospodarskim panogam bi takšen material bil zanimiv.
Potem smo se povezali še z reciklatorji oziroma predelovalci določenih odpadnih materialov. Ta ideja se nam je zdela dobra za izvedbo mednarodnega projekta sploh zdaj, ko smo v obdobju tranzicije krožnega gospodarstva.
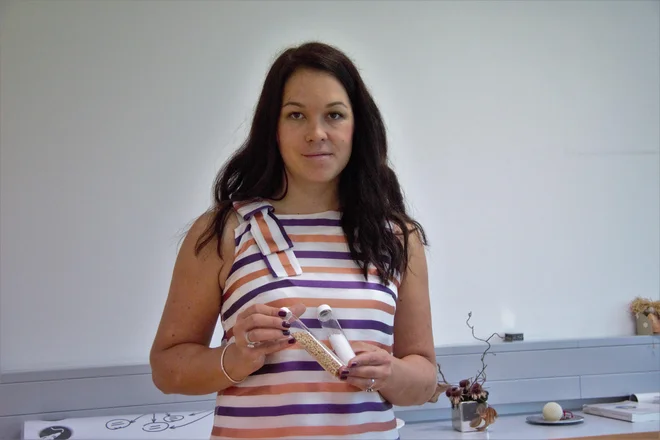
Vesna Žepič Bogataj
Ali pri tem potrebujete tudi znanje drugih strok?
Seveda. Spraviti v en kompozit les in plastiko je težko, ker komponenti nista kompatibilni – les je hidrofilen, plastika je hidrofobna. Na lesnih komponentah morajo biti narejene nekatere modifikacije, bodisi kemijske na površini celuloznih vlaken bodisi mehanske z dodatki kompatibilizatorjev v obliki granulata, da dobimo ustrezno spojnost komponent in homogeno obliko izhodnega kompozita. Kemični modifikaciji prve ali druge materialne komponente se v tem projektu načeloma izogibamo, ker racionalno ni prenosljiva v nobeno industrijo …
Sodelujejo torej kemiki, procesna industrija za ekstruzijsko pripravo kompozitnega granulata, potem potrebujemo orodjarje, da izdelajo ustrezna orodja, sledijo še tehnične odobritve materialov po določenih standardih in certifikatih. Potrebujemo torej obsežno interdisciplinarno znanje.
Za projekt Ceplafib so podjetja očitno bila zainteresirana.
Vsi okoljsko naravnani projekti Life, ki smo jih v Tecosu prijavljali, so naravnani tako, da so na koncu čim bliže trgu. Ne razvijamo bazičnega znanja, temveč je to po koncu projektov takoj uporabno in prenosljivo na industrijsko raven. Ceplafib smo predstavili našim podjetjem in iskali nekoga, ki bo znal reciklirati odpadno plastiko, nekoga, ki lahko pripravi surovine za ojačitve, regenerirana celulozna vlakna iz odpadnega papirja ali iz naravnih ligno-celuloznih virov poljedelskih odpadnih produktov … Našli smo ga na Finskem, kjer se veliko podjetij ukvarja s predelavo lesnih surovin.
Ugotavljamo, da se je tudi slovenska industrija zbudila in sledi krožnim zgodbam.
To sta bila prva partnerja. Nato smo iskali tehnološke centre, da pomagajo pri procesnih tehnologijah in nazadnje še, koga bi takšni izdelki zanimali. Vzpostavili smo stik z Adrio Mobil, ki v avtodome in prikolice vgrajuje okoli 35 odstotkov komponent iz plastike. Zanimalo jih je. Njihove glavne zahteve so bile povezane z mehansko in strukturno trdnostjo materiala, kar jim narekujejo standardi o varnosti voznikov in potnikov. Za končne izdelke smo predvideli pokrivne panele za skrite inštalacijske sisteme, notranji dekor, ker jim je bila všeč vidna struktura lesnih vlaken v plastiki. Druga aplikacija uporabe novega kompozita bo izdelava distančnih profilov za dvojni pod v avtodomih. Zdaj so iz lesa. Serijska proizvodnja brizganih distančnikov iz lesno-plastičnih kompozitov bo okoljsko boljša.
So takšni deli tudi ekonomsko ugodnejši?
V Omaplastu pravijo, da je reciklirani polipropilen cenejši. Novi kompozitni materiali bodo cenejši, ker bomo uporabili cenejše reciklirane surovine. Če za polnilo uporabimo vlakna iz časopisnega papirja, dobimo tudi lažji material in porabimo 30 do 40 odstotkov manj plastike.
Potreben pa je ves krog, od ločenega zbiranja odpadkov, izdelave granulatov, veliko je transporta, ustvarja se ogljični odtis. Pravite, da bi lahko za 40 odstotkov znižali izpuste … Se tudi z upoštevanjem vsega tega izračun izide?
Da. Naš glavni cilj je obvarovati primarne vire, saj je plastika v osnovi narejena iz naftnih derivatov. Z vnosom reciklatov v končni kompozitni material zmanjšamo ogljični odtis. Izdelali pa bomo tudi študijo ustvarjenega odtisa od surovine do končnega izdelka.
Za kakšno uporabo pa gre v gradbeništvu?
Gre za notranje akustične panele, odrske panele, ki bi zamenjali USB-plošče. V gradbeništvu je uporaba lesno-plastičnih kompozitnih materialov že znana. Izdelujejo na primer fasadne plošče, terasne pode, obrobe bazenskih kompleksov … Novost tega projekta je uporaba lesno-plastičnih kompozitov, ki so v celoti izdelani iz recikliranih surovin.
Za industrijsko embalažo se reciklirani materiali že uporabljajo.
Ne gre za primerljivo embalažo. Podjetje Ecopulp iz Finske zdaj obvladuje izdelavo celuloznih embalažnih izdelkov z vročim stiskanjem, ker pa v svojih produktnih linijah potrebuje tudi trša embalažna ogrodja, se mu je skozi projekt Ceplafib ponudila priložnost za uvedbo trših, vendar kljub vsemu v celoti reciklabilnih materialov.
Ceplafib je že četrti tovrsten projekt Tecosa, prvega ste opisali, s čim pa se je začelo?
Od 2015 do lani nam je v treh zaporednih letih uspelo pridobiti evropska sredstva za zagon treh do okolja prijaznih Life projektov in ugotavljamo, da se je tudi slovenska industrija zbudila in sledi krožnim zgodbam. V prvih projektih iz let 2015 in 2016 je Tecos sodeloval kot partner, pri sedanjem pa je koordinator. Prvi projekt, Life Baqua, ki ga koordinira španska univerza s Kanarskih otokov, temelji na uvajanju krožnih rešitev za izrabo bananinih odpadkov za razvoj produktov v ribogojskem in plastičarskem sektorju. Na Kanarskih otokih imajo ogromne plantaže bananovcev, oleseneli stebelni ovoji palm pa se v velikih količinah leta dolgo kopičijo na tleh. Ideja projekta Baqua je predelava olesenelih ostankov bananovcev v vlakna za ojačitev strukturno polimernih izdelkov v avtomobilski industriji ali industriji bele tehnike. Odpadni produkti bananovcev bodo obenem predelani v granulirano hrano za ribe na bližnjih morskih gojiščih.
Vsi okoljsko naravnani projekti Life, ki smo jih v Tecosu prijavljali, so naravnani tako, da so na koncu čim bliže trgu.
Novomeško podjetje Ambi-Metalplast, ki izdeluje brizgane plastične dele za avtomobilsko industrijo, je partner tega projekta in želi v svoj nabor vključiti tudi izdelke iz takšnih sonaravnih materialov.
Drugi projekt, Life Citruspack, se je začel leta 2016. Pobudnik je špansko podjetje AMC, ki izdeluje sokove iz agrumov in ima ogromno odpadnih surovin. Vodilni partner projekta je raziskovalni center AITIIP iz Zaragoze, sodelujejo pa še raziskovalni in industrijski partnerji iz Španije, Belgije, Slovenije in Francije. S pomočjo kemične ekstrakcije bodo iz odpadnih ostankov citrusov, olupkov in pulpe, pridobljene netopne antioksidantske spojine, ki bodo uporabljene kot dodatek kozmetičnim produktom za efekt pilinga ter surovinska baza za izdelavo naravnih ojačitev v biorazgradljivih polimernih osnovah za izdelavo biokompozitne embalaže za plastenke za sokove in lončke za kreme.
Ceplafib je edini od treh projektov, kjer material ne bo biorazgradljiv in ga bo treba ločeno zbirati.
Da, bo pa ločeno zbran spet uporaben za recikliranje. Evropa zahteva, da morajo biti do leta 2030 vsi izdelki iz plastike reciklabilni. Naš material bo reciklabilen vsaj kot polnilo.
Sodelujete s Finci, Španci in drugimi, poznate razmere na področju recikliranja v Evropi. Kje je Slovenija?
Ni tako slabo, kakor včasih mislimo. Slovenija je pri reciklaži vseh vrst odpadkov tretja v Evropi po deležu zbranega stekla, plastike, papirja … Pri reciklaži plastike prednjačita Nemčija in Češka, reciklirajo je več kot 45 odstotkov. Slovenija je že med 40 in 45 odstotki. Novomeški Omaplast, ki je reciklator plastike, dobiva odpadno embalažo večinoma iz tujine, v Sloveniji le desetino. Potrebuje čiste materiale, in ne mešanih vrst plastik, te pa je najlaže dobiti iz industrije.
Kaj pomeni prepoved uvoza odpadkov na Kitajskem?
Kitajska je januarja letos uvedla zeleno zaveso in prepovedala uvoz 24 vrst odpadkov. Včasih je bila zlata jama za izvoz odpadkov, od tam pa smo dobivali poceni komponente. Zdaj ni več tako. Odpadne plastike iz tujine sploh nočejo reciklirati, niti odpadnega kartona. To je lahko težava, lahko pa tudi nova priložnost za evropsko območje. Lahko se bo pojavilo več podjetij, ki se bodo začela ukvarjati z reciklati. Tudi Omaplast v tem vidi priložnost.
Velenjsko podjetje Skaza uporablja biorazgradljive reciklate in pravijo, da večino po želenih recepturah dobijo iz Italije.
Slovenija nima veliko proizvajalcev granulatov iz odpadne plastike. Eden izmed ciljev našega projekta je, da Omaplastu odpremo poti do kupcev v Evropi tudi tja, kjer še niso prisotni, in tudi do boljšega sodelovanja s slovenskimi proizvodnimi podjetji. Zato smo k Ceplafibu povabili še druga podjetja in doslej se jih je pridružilo dvanajst. Med njimi je osem slovenskih, ki jih novi material zanima – ali kompozit iz reciklirane plastike in časopisnih vlaken, morda samo reciklirani plastični granulat … Med njimi so Gorenje, Bokri, Isokon, Koplast, Plastoform, Skaza, Snaga, Vivapen … Povabilo je odprto, zmogljivosti imamo dovolj, da lahko novega materiala izdelamo več. Ne torej samo za potrebe našega projekta, temveč za vse, ki bi želeli preizkusiti nov kompozit v svojih utečenih produktnih linijah.
Čas apliciranja vaših projektov, tudi Ceplafiba, prenosa in aplikacije znanja v gospodarstvo, je izjemno kratek.
Znanje se je razvijalo in nalagalo že prej, je pa tri leta za nov material z vso akreditacijo na trg in uporabo na procesnih strojih res kratko. Mi smo po tem, ko smo vedeli, da so vsi potrebni materiali na voljo, nov kompozit razvili v letu dni, še dve leti pa sta potrebni za validacijo.